World-first fossil-free steel manufacturing plant completed in Sweden.
The global production of zero emissions steel has taken a massive step forward, with a world leading Swedish project completing the construction of a world-first fossil-free steel pilot plant in Luleå, Sweden.
Three Swedish firms came together to form an innovative partnership around the HYBRIT project, which has integrated the supply of raw material, steel processing and energy supplies into a single project, that could be the gateway to the decarbonisation of the currently coal dependent steel industry.
The partnership, which includes LKAB, SSAB and Vattenfall established the HYBRIT project, with the aim of producing emissions free steel and cutting Sweden’s greenhouse gas emission by as much as 10 per cent in the process.
SSAB is one of the world’s largest steel manufacturers and has partnered with iron ore producer LKAB, and electricity company Vattenfall, to undertake the HYBRIT project as a validation of the green steel manufacturing process.
“I’m incredibly proud that our globally unique pilot plant has now been completed. It is a milestone in the transition to fossil-free steel. We aim to be the first to market, in as early as 2026, with fossil-free steel,” President and CEO of SSAB Martin Lindqvist said.
“HYBRIT technology will enable us to eliminate carbon dioxide emissions in steelmaking and at the same time help our own customers to reduce their climate footprint. We have the chance to revolutionize the entire steel industry and show that net-zero emissions is possible. We must seize this chance.”
The project has set itself the goal of bringing zero emissions steel to market by 2026, and considers that it could be possible to transition to a completely emissions-free steel manufacturing sector in Sweden within the next 20-years, and has the support of the Swedish government to make that happen.
“Right now we have a historic opportunity to do things that provide jobs here and now – but also hasten the climate transition that everyone realises is necessary,” Swedish prime minister Stefan Löfven said.
“Today, you are laying the foundations that will enable the Swedish steel industry to be entirely fossil- and carbon dioxide- free in 20 years. Together we can rebuild Sweden as the world’s first fossil-free welfare nation.”
Swedish climate change minister and deputy prime minister, Isabella Lövin said that the project should hopefully lead to a transformation across the global steel manufacturing industry.
“This inauguration concretizes that the industrial transition is taking place as we speak, and that a fossil-free society is within reach. This unique project has generated a lot of international attention for Sweden. Through the Leadership Group for Industry Transition, which the UN has asked Sweden to lead, this has the opportunity to reverberate around the world,” Lövin said.
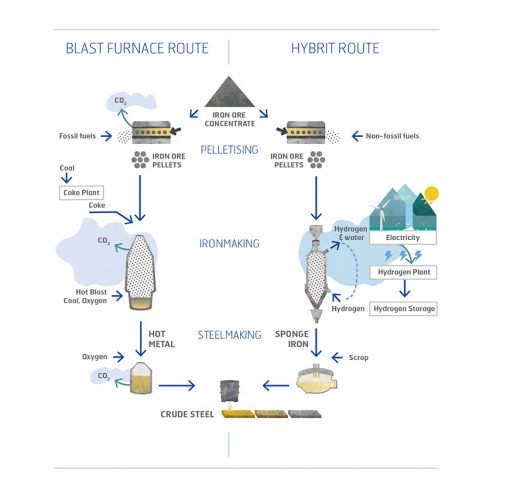
The Swedish government owned Vattenfall is supplying renewable electricity to the plant, that is used to produce the zero emissions hydrogen that is in turn utilised in the steel manufacturing process.
Vattenfall’s CEO Magnus Hall said that by incorporating hydrogen into the steel manufacturing process, there are advantages both in terms of emissions reductions, as well as an opportunity to strengthen the overall energy system by using hydrogen as an energy storage medium.
“A partnership like this shows how we can take the lead in the transition to innovative, fossil-free products. Vattenfall seeks to enable a fossil-free life within a generation, not just through fossil-free production but also through partnerships like HYBRIT, where we can use electricity as a source of innovation for a fossil-free future,” Hall said.
“Our fossil-free electricity and its conversion to hydrogen are key components here, not just for the steel but also because the storage of hydrogen can balance an electricity system with more weather-dependent power generation and increased capacity challenges. I am proud that everyone involved has made it possible to start up this plant today and I look forward to seeing fossil-free steel on the market.”
Traditional steel manufacturing processes are highly dependent on the use of coal, both as a source of high temperature heat, as well as a source of carbon necessary in the steel production process.
Construction of the HYBRIT facility commenced in 2018 and was completed in just over two years with financial support from the Swedish Energy Agency. The HYBRIT project will undertake a number of commissioning trials at the newly completed plant, which will be able to produce around one-tonne of steel each hour.
Steel manufacturing is responsible for an estimated 7 per cent of global emissions and has often been cited as a challenging sector to decarbonise due to the need for high temperature heat, not easily produced from wind and solar resources.
The HYBRIT project will seek to validate the alternative means of producing steel using green hydrogen as an intermediary step, allowing zero emissions electricity to effectively displace coal in the steelmaking process.
The project could have significant implications for the Australian steel and coal industries, both as a first step away from the use of coal as an input in the steel manufacturing process, but also as an example of how countries can take advantage of generous wind and solar resources to produce zero emissions materials.
*Michael Mazengarb is a journalist with RenewEconomy, based in Sydney. Before joining RenewEconomy, Michael worked in the renewable energy sector for more than a decade.
1 September 2020
RENEW ECONOMY